Shanghai--(Business Wire)—Henkel is offering a unique, fully automatic impregnation solution to repair casting parts with various porous defects such as air holes, needle holes and shrinkages, so as to save cost for customers. Impregnation is a technology to address micropore-caused leakage in casting parts by filling thin fluid to the micropores under normal or elevated pressure, which will solidify and polymerize in order to seal up the pores.
Henkel impregnants
Henkel Loctite impregnants are two types of methacrylate resins: heat curable and oxygen-weary. Resinol 90R,Resinol 90C,Resinol 88 are all heat curable, among which 90R is Henkel’s new recyclable resin. Resinol RTC and Fleseal 5100 are oxygen-weary products with the latter being specially developed to seal up pores on electron components. 90R, due to its lower density than water, can therefore be separated from the washing water. With the 90R impregnation process, 85-90% of the resin washed away by water can consequently be recycled, greatly saving the impregnant that is otherwise to be wasted. Meanwhile, compared to the impregnation process of non-recyclable heat curable resin, the water consumption of 90R can be reduced by 40%, thus saving cost for sewage treatment. Currently all Henkel Loctite Impregnation Service Centers use the recyclable resin 90R in their casting impregnation services.
Impregnation process
Vacuum pressure impregnation is the most widely used and most effective method for one-piece impregnation, as is demonstrated in Graph 1. The process of pressure impregnation can be done under normal pressure for convenience purpose.
When the components are put in the vacuum impregnation tank, the tank will be vacuumed first to get rid of air and particulates. This step is called dry vacuum, during which the pressure would normally drop below 80mbar. Dry vacuum will last 5-10 minutes then the tank will be filled with the impregnant, vacuumed and stay vacuumed for another 5-10 minutes, which is called wet vacuum, aiming to get rid of the air in the impregnant so as to prevent the air-dissolved impregnant from infiltrating into the components’ pores and causing air holes which will affect the sealing effect when solidifying. After wet vacuum, the tank will be pressurized to press the impregnant into the pores. Normally, the air pressure should be raised to 0.5Mpa and be kept for 5-10 minutes. Pressurization is not mandatory in this process. 5-10 minutes of impregnation under normal pressure is also acceptable. After impregnation, the impregnant residue on the components’ surface or in the pores will be spun out by a centrifugal force and rinsed. Finally, the components will be placed in in 90°C water for 10-20 minutes for the impregnant to solidify in the pores.
Impregnation equipment
Henkel Loctite impregnation process uses the independently developed automatic fast impregnation equipment (Graph 2), which is comprised of a vacuum tank (the lower part is resin tank), a dripping tank, a washing tank, a rinsing tank, a solidifying tank and a recycling device. The recycling device is connected to the washing tank with the washing water circulating in between. The impregnation process is controlled by Programmable Logic Controller (PLC) whose touch screen can dynamically display every single process including liquid level, pressure, temperature and valve switch. The components basket can be moved freely among the tanks by the robot arm. The whole impregnation process is unmanned. Compared to the popular slotted equipment, Henkel’s automatic fast impregnation equipment can guarantee the consistent impregnation quality and increase the process speed to five baskets per hour.
Impregnation quality
The impregnation quality is judged from three aspects, namely the sealing rate, impregnant residue and physical damage like bumping cruise, erosion and oxidation staining.
The impregnation technology only seals pores and exempts big holes because the resin can flow away from the big holes, particularly during the solidifying process. Therefore, the size of the pores of the components is critical in determining the sealing effect. For a specific process and impregnant, the longer the pore is and the smaller the pore diameter is, the longer it takes to fill the pore. Theoretically, Henkel impregnation resin and process can seal a pore with a maximum diameter of 0.25mm.
The impregnation quality is closely related to the impregnant, the impregnation process and the impregnation equipment. To ensure a high sealing rate, the impregnant quality must be monitored regularly. Henkel Loctite Impregnation Service Center monitors the impregnant in terms of polymerization time, density and viscosity, to ensure the good quality.
If the resin residue in the components’ screw-threads or other blind holes is not rinsed completely, it will be hardly possible to be removed after solidification, thus hampering follow-up casting or processing. The components’ placement, the rinsing method and time, the quality of the washing water and the centrifugal force all affect the final cleansing effect. Placing the concave surface and blind holes downward or outward can help spin out the liquid during the centrifugal process. In addition, replacing the water in the washing tank and solidifying tank regularly, increasing the rinsing time and frequency and increasing the centrifugal time and rotate speed also help enhance the cleansing effect. Henkel Loctite Impregnation process has designed a centrifugal procedure following the process in each tank to spin out the impregnant residue and water. The water in the rinsing tank is also monitored with regular water replacement and tank wall cleaning. The resin separation test is performed each week to inspect the content of water and resin in the washing tank. If the volume of the resin layer on the water larger than is 12% of the water, the resin-removal process should be conducted to improve the washing effect.
During the impregnation process, the casting components are prone to oxidization and erosion when rinsed in water or solidifying under high temperature, antioxidants and preservatives must be added to the washing tank and the solidifying tank to avoid staining caused by oxidation and erosion.
Henkel impregnation system leverages the hi-tech resins to guarantee a stable quality and incomparable sealing performance. Henkel’s effective impregnation solution helps customers achieve a higher level of sustainability by reducing resin waste, energy cost and processing time.
Contacts:
Echo Liu
Regional Marketing Communication Manager
Office: +86 21 2891 5832
Email: echo.Liu@henkel.com
Neil Zhu
Business Development Manager, Asia Pacific
Mobile: +86-13636348685
Email: neil.zhu@henkel.com
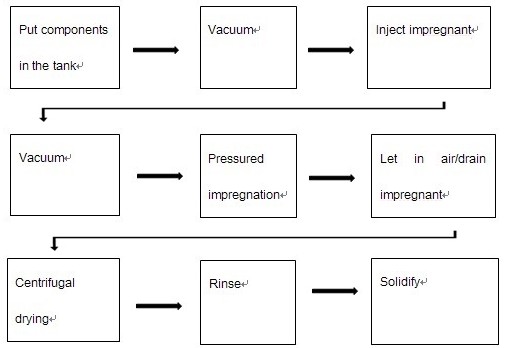
Graph 1. Vacuum pressure impregnation process

Graph 2. Henkel Loctite fast automatic impregnation equipment